Тихвинский вагоностроительный завод - ведущее российское предприятие и один из крупнейших мировых производителей железнодорожного транспорта - задаёт новый тренд на рынке вагоностроения. О том, какое значение имеют инновационные технологии, каким образом они делают завод независимым от зарубежных поставок, и какие обязательства накладывает на предприятие роль самого крупного работодателя региона, рассказал генеральный директор завода Геннадий Веселов.
Машиностроительный кластер
Елена Бевза: - Тихвинский завод - молодое предприятие, но с корнями из советского прошлого. Раньше на этой площадке размещалось машиностроительное предприятие. Как принималось решение о создании вагоностроительного завода?
Геннадий Веселов: - История завода началась в 1963 году, с началом строительства в городе завода литья и металлоконструкций, задачей которого было обеспечение литейной продукцией Ленинграда и всего Северо-Запада. Позднее завод вошёл в состав объединения «Кировский завод» и перешёл на выпуск комплектующих для трактора «Кировец». Здесь производили широкую номенклатуру продукции - от товаров народного потребления до изделий оборонного назначения. Не было ни одного технологического процесса, применяемого в машиностроении, который не использовался бы на Тихвинском заводе - литейное, кузнечно-штамповочное, инструментальное, гальваника. В конце 80-х численность работающих достигала 22 тысяч человек. В 90-е отсутствие спроса на отечественные тракторы вызвало необходимость поиска другого направления развития. Было выбрано железнодорожное машиностроение. В Тихвине стали производить узлы и детали железнодорожной техники, создавались и единичные продукты, такие как щебнеочистительная машина. В начале 2000-х на заводе был построен опытный образец высокоскоростного электропоезда «Сокол-250». Всё это способствовало принятию в 2006 году решения о постройке на базе Тихвинской промплощадки современного вагоностроительного производства. 30 января 2012 года в присутствии президента России Владимира Путина состоялся запуск Тихвинского вагоностроительного завода.
- Какова мощность предприятия?
- В 2012 году мы выпустили 1300 вагонов. В прошлом - уже более 15 000. За четыре года выпуск увеличен более чем в десять раз. Сегодня суммарная мощность производств в Тихвине - 22 тысячи вагонов в год, что позволяет позиционировать нас как мирового лидера в производстве вагонов.
Применяя мировой опыт
- Чем отличается ваша продукция от продукции других производителей?
- Мы выпускаем вагоны нового поколения с улучшенными характеристиками. По своим потребительским свойствам, экономической эффективности и надёжности наши вагоны во многом превосходят продукцию конкурентов. Наши преимущества - повышенная грузоподъёмность, уменьшенная масса самого вагона, увеличенная скорость движения, прочность и долговечность. Сейчас на путях страны ходит почти 50 000 тихвинских вагонов.
- В чём суть инновации?
- Мы сделали ставку на наукоёмкое производство. В создании завода участвовали ведущие мировые компании из более чем пятнадцати стран. Литейное и вагоносборочное производства оборудованы роботами и автоматическими линиями. Есть много оборудования, не имеющего аналогов в мире. Совокупность высокой степени автоматизации, применения современных технологий и использование мирового конструкторского опыта и практик позволили представить на рынок продукт, задающий новые тренды в отечественном вагоностроении. Мировой опыт поставлен на службу стране. Мы взяли лучшую и самую распространённую в крупнейших железнодорожных странах - Северная и Южная Америка, Китай - технологию создания ходовой части вагона, так называемой тележки, и адаптировали её к нашим условиям эксплуатации.
- Что и позволило вам занять 40% отечественного вагоностроительного рынка?
- Да, в этом заслуга нашего инновационного продукта. Покупатель выбирает товар с наилучшими эксплуатационными свойствами. Создание новой тележки позволило нам также увеличить межремонтный пробег вагона до 8 лет, или до 800 тысяч километров.
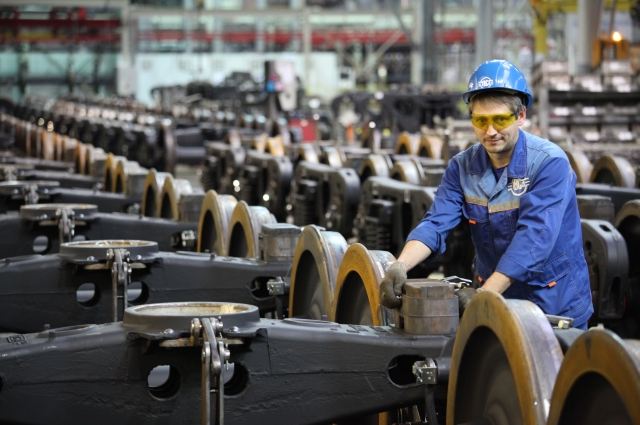
Импортозамещение
- Но это ещё далеко не все ваши инновации. Другой стало производство высокопрочного чугуна.
- Да, это уникальный технологический процесс, который мы освоили впервые в России. Дело в том, что у тележки вагона есть быстро изнашивающиеся элементы. Для их создания применяется особый материал - высокопрочный чугун. В России не было производителя нужного нам металла, мы поставляли его с американского рынка. В прошлом году, понимая, что зависимость от заокеанского партнера скажется на производстве, закупили американское оборудование и, используя российское сырье и лучшие мировые технологии, приступили к собственному выпуску изделий из высокопрочного чугуна. Всё, что мы планировали по объёму и срокам, у нас получилось. Это серьёзное достижение с точки зрения развития внутренних компетенций страны. Компания КамАЗ, узнав, что мы начали такое производство, обратилась к нам за помощью в изготовлении необходимых деталей и для них.
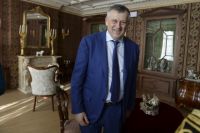
- Завод такого масштаба просто обязан применять природосберегающие технологии. Как вы решили, например, проблему отвалов в литейном производстве?
- В своё время под них использовалась значительная часть земель промышленной площадки, такова была технология литейного производства времен СССР. Сейчас у нас отходов нет за счёт того, что применяем уникальную систему формовки с помощью вакуума. Связующим элементом пескообразующей смеси у нас выступают не смолы, не лаки, а вакуум. После снятия вакуума литейная форма превращается снова в песок, который опять идёт на изготовление форм. Это один из элементов экологической программы повышения эффективности использования ресурсов.
- Ваши вагоны закупают крупные компании: «Кузбассразрезуголь», «Сибирская угольная энергетическая компания», «Уралхим».
- Да, основными заказчиками выступают предприятия добывающей промышленности, прежде всего угольных разрезов. Мы выпускаем четыре основные модели: полувагоны, хопперы, платформы и цистерны для перевозки наливных грузов. Работаем с учётом потребностей заказчика. У завода полный цикл изготовления - от составления технического задания, согласованного с конкретным потребителем, до выпуска вагона и обслуживания его в эксплуатации.
Учебный центр
- В прошлом году социальные расходы завода составили около 300 миллионов рублей.
- Социальная программа для нас ключевая. Мы вкладываем средства в поддержание достойных условий труда. Сотрудники, работающие на литейном, сборочном, сварочном производстве, получают дополнительную надбавку за вредность, имеют сокращённый рабочий день и другие привилегии в соответствии с законодательством. У нас большая жилищная программа, которая предусматривает до 50% компенсации затрат на обслуживание ипотеки. Все сотрудники, отработавшие больше трёх лет, имеют право на дополнительное медицинское страхование за счёт работодателя. Мы доплачиваем за питание в столовых, бесплатно доставляем персонал из близлежащих городов. Мы дорожим своими людьми и по-прежнему нуждаемся в высококвалифицированных кадрах. Ведём их поиск во всех регионах Российской Федерации.
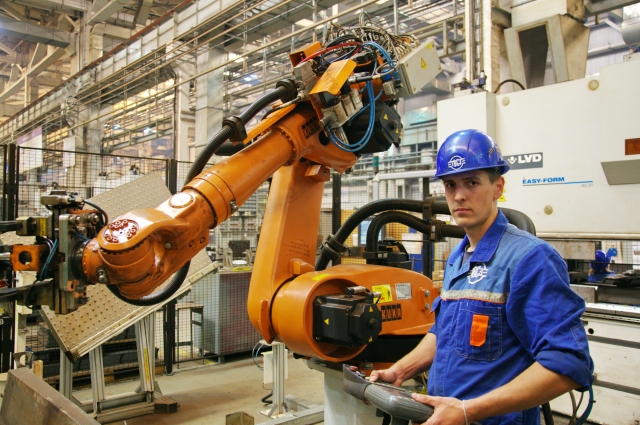
- А как обучаете?
- У нас сложное оборудование и технологии, а это требуют особой подготовки персонала. Мы создали собственный учебный центр, где обучаем всем необходимым для нас специальностям. Показатель прироста объёма выпуска продукции говорит о том, что нам удалось решить эту задачу.
- Предприятие, наверно, участвует и в городских социальных программах?
- Безусловно, ведь наши сотрудники - жители Тихвина. От того, как они проводят своё свободное время, во многом зависит эффективность их труда. По соглашению с городом мы ежегодно инвестируем в развитие его инфраструктуры - ремонт дорог, спортплощадок и благоустройство городских пространств. Есть у нас и собственные проекты. Например, создали библиотеку нового поколения - социокультурный центр «Тэффи», где совмещаются классический способ работы с книгами с электронными методами получения информации. Другой проект - фестивальная площадка, зона отдыха, которую мы организовали в центре города рядом с исторической частью Тихвина.